What lessons can logistics and supply chain companies learn from the COVID-19 crisis?
As we collectively navigate our way through the social and economic crisis caused by the COVID-19 pandemic, it is important to remember that for every challenge we encounter, there is also a lesson to be learned. The individuals and companies that adopt a growth mindset, with a commitment to uncover the lessons in this challenging time, are those that are best positioned to weather the storm and continue to thrive long after we have overcome the virus.
Ready to digitize and modernize your freight forwarding operations?
See how Magaya can help.
“In the midst of every crisis, lies great opportunity.”
– Albert Einstein
Although it has only been a few weeks since social distancing measures and stay at home orders have been widely in place in most states, there have already been significant impacts on supply chain and logistics businesses. As Deloitte puts it, “The COVID-19 pandemic is a global crisis without modern parallel. The lack of precedent for a black swan event so broad in its impact across geographic, demographic, and economic sectors explains why many public and private sector organizations were already becoming strained before the World Health Organization (WHO) officially declared a pandemic on 11 March 2020.”
The World Ports Sustainability Program has already reported an increase in demand for warehouse storage for food and medical supplies at 35 percent of ports. At the same time, 40 percent of ports surveyed have experienced a 5 to 10 percent decrease in port calls, while 14 percent of ports have seen a 25 percent drop in port calls. Demand is shifting at an astonishing pace and will continue to see highs and lows as the situation unfolds in the months ahead.
Supply Chain Challenges Due to COVID-19
“75 percent of companies report supply chain disruptions in some capacity due to coronavirus-related transportation restrictions, and more than 80 percent believe that their organization will experience some impact because of COVID-19 disruptions.”
Institute for Supply Management
Rapid shifts in demand leading to unforeseen increases or decreases in volumes in various product categories are not the only challenges COVID-19 has brought upon the American supply chain.
Stores have struggled to meet demand for certain product categories as consumers rushed to stockpile essentials.
In addition to extreme shifts in demand and volumes, other challenges have included:
- Evolving trade restrictions
- Manufacturing slowdowns and restrictions
- Import-export and port delays
- Increased employee absenteeism
- Border shutdowns
- Social distancing requirements
These all pose significant hurdles for logistics and supply chain businesses. There remains a lot of uncertainty in our future, and surely more challenges will present themselves, but there are already many lessons to be learned from the situation to date.
Lessons of COVID-19 for Supply Chain Companies
According to Deloitte, there are typically three phases that will unfold as we move through and overcome a crisis:
Respond – the acute crisis in which risk management and ensuring basic business continuity is the main priority
Recover – the recuperation period that follows the height of the crisis
Thrive – companies that have learned the right lessons and executed on their learnings will thrive in the “next normal”
While we have never seen a global crisis on the level of COVID-19 in modern times, there are some fundamental qualities of companies that contribute to their resilience in the face of threats and challenges. COVID-19 is giving us all a masterclass in what it takes to survive, recover from, and, ultimately, thrive after a major crisis. Although we are still in the Respond phase, we can already observe a number of commonalities among the businesses that are faring the best:
Adaptability and Agility – Companies that have had the agility to adapt the fastest to unforeseen circumstances are faring well through the Respond phase. Whether it’s pivoting quickly to remote work thanks to Cloud-based logistics software systems, or implementing new around-the-clock shifts to maintain business continuity in the face of new social distancing regulation, companies need to be more agile and adaptable now than ever before.
Having a real-time, holistic view of your enterprise is also important to enable swift action in the face of rapid change. Supply chain businesses need to be agile enough to weather a temporary drop in volumes, but also prepare for a spike when certain sectors begin to reopen and recover. From one day to the next, regions may choose to reopen some retail sectors, and companies must be ready to adapt their business processes quickly where needed.
Transparency and Communication – During any crisis, it’s important to communicate openly and often with all stakeholders: employees, customers, and business partners. Leading companies are being transparent about the measure they’re taking to adapt where needed via website, email, social media, and more. It’s important to reassure stakeholders that there’s a plan in place and to address challenges honestly. Transparency now builds trust in the long run.
Building and communicating with a strong network of business partners also helps businesses to adapt in the face of crisis. You’ll need a plan A, B, and C for many processes and may need to call on new partners to ensure supply chain continuity. That’s why Magaya has built in the Magaya Network to our software. This communication platform allows customers to connect and exchange data electronically with a worldwide network of potential supply chain partners.
Efficiency and Automation – Organizations that have effective automation and customer self-service tools in place are able to rapidly scale to meet shifts in demand and workload. One example is a self-service supply chain tracking and visibility tool like Magaya LiveTrack that lets customers see the status of their shipments without needing to contact an already-overburdened customer service team.
Another example is Magaya Dimensioner, a hardware solution that automates the time-consuming task of pallet or parcel dimensioning, letting you process far more cargo in less time than it would take to do so manually. With the right processes, tools, and technology in place, the business is able to scale as needed without eroding profits. This also puts the company in a strong position to be able to capitalize on unexpected opportunities that may arise, such as surges in demand for certain product categories or services, like last-mile logistics.
Customer Focus – Loyal customers are your best asset. At the end of the day, your customers are what keep your business going. All of the above points have one thing in common: they all contribute to creating a positive customer experience, even though life’s greatest challenges. Maintaining a strong customer focus, putting your customers’ needs at the center of every decision you make, will not only enable you to get through the crisis, but will prepare you to thrive and grow in the long term.
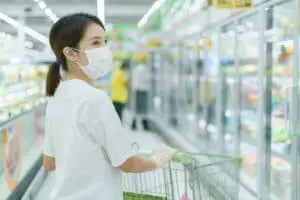
The retail industry will undergo major changes as we learn to live with COVID-19.
Although recent times have brought about enormous challenges, if we focus on learning and growth, we will overcome, recover, and emerge stronger in the face of great adversity.
Ready to digitize and modernize your freight forwarding operations?
See how Magaya can help.